Introduction: Product and Market Overview
Passive electronic components considered as specialty parts are high dollar, low volume products whose pricing is secondary to quality. These products have the highest operating margins and represent the smaller percentage of global passive component revenues, accounting for about 13% of global capacitor, resistor and inductor revenues in fiscal year 2015.
In this MarketEYE article, we take a closer look at specialty passive components that are consumed in value-added and application specific market segments on a global basis. Such components are generally consumed in high voltage, high frequency, high temperature, high reliability or harsh environment applications where their performance is mission critical and there is an expectation on behalf of the design engineer that component failure is highly unlikely as long as the components are installed properly and used within the manufacturer’s guidelines.
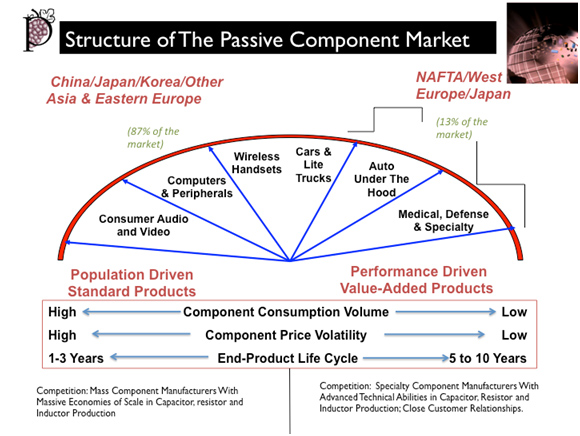
Source: Paumanok Publications, Inc. All Rights Reserved
Key end-markets where specialty components are consumed include a myriad of fragmented segments that can broadly be categorized under the following designations: automotive under-the-hood electronics, specialty power supplies, specialty lighting ballasts, defense electronics, aerospace electronics, medical electronics, welding electronics, instrumentation and control equipment electronics, telecommunications infrastructure equipment, marine electronics (including undersea cable), mining electronics, railroad electronics, nuclear power plant electronics and down hole pump and oil and gas equipment electronics.
As we have noted in the chart above, the specific criteria associated with the specialty passive component markets are as follows.
13% of global consumption value for all passive components is specialty in nature.
Specialty component markets can largely be found in the United States, Germany, Japan, UK, France, and Korea
Component shipment volumes are low
Component prices are high
Component price volatility is limited
End-product life cycles are usually 5 to 10 years or more
Vendors have advanced technical capabilities and close customer relationships
Products are usually high voltage, high frequency or high temperature in nature and in many instances a combination of these criteria is inherent in the parts.
High Voltage Passive Components
High voltage passive electronic components are defined as capacitors, resistors and inductors that are rated for circuit operation at 100 Vdc or greater for the purposes of this article. Ceramic chip capacitors, for example, are typically applicable in circuits to 5 kV, and represent the largest market segment, followed by product markets between 5 and 20 kV, whereby the majority of these applications are almost exclusively single layer discs, or multilayered radial leaded capacitors in design and seldom exceed 20 kV. Ceramic capacitor applications greater than 20 kV are “doorknob” type products, otherwise known as valve block designs and maximize out at approximately 100 kV. The other type of capacitor consumed in high voltage applications to 100 kV is the polypropylene type plastic film capacitor, which is usually the capacitor of choice in power transmission and distribution applications for power factor correction and also for burst power. Aluminum electrolytic capacitor large can designs are also consumed in high voltage applications, such as traction applications, up to approximately 500 volts. Tantalum capacitors, on the other hand, are seldom used in high voltage applications, but recent breakthroughs in tantalum technology have allowed dry-type tantalum capacitors to be used in specialty medical applications up 300 volts.
In resistors there are many types of high voltage configurations and resistive elements employed. In thick film chips, high voltage ruthenate pyrochlore resistive inks are used on ceramic substrates to achieve a high voltage surface mount resistive product top 3 kV. Axial and radial leaded resistors employing tin-oxide are also used in high voltage applications up to 8 kV, and thin film nickel chromium resistors are also employed in applications up to 1 kV. The highest voltage resistor by type is the axial leaded carbon film resistor which is applicable to 40 kV.
High voltage inductors represent a small part of the overall discrete inductor market, but we note that there is demand for wirewound inductors for applications to 400 Volts.
The majority of specialty power supply applications that require high voltage passive components within the definitions described here are for ultimate consumption in the test equipment market, the medical test and scan equipment market, the medical implant market, the semiconductor manufacturing equipment market and the defense and aerospace electronics industry. The defense and aerospace markets are primarily for applications in pulse forming radar, missile power up, satellites and space probes and in various laboratory test environments.
Some high volume applications, for larger volume consumption exist in the form of safety capacitors for interference suppression in line voltage equipment (i.e. smoke detectors, fire alarms and lighting ballasts (from 100 to 2500 Vac) 630 Vdc tip and ring applications for telecom infrastructure (i.e. in subscriber line interface cards), or in unusual market segments, such as undersea cable transmitters, TV transmitters, and pumped lasers.
Specialty power applications requiring high voltage passive components include power transmission and distribution capacitors, certain types of motor run capacitors, microwave oven capacitors, welding capacitors, traction capacitors, furnace capacitors, and DC link capacitors for renewable energy systems and for hybrid electric vehicles.
High Frequency Passive Components − UHF, SHF and EHF
The majority of product applications for high frequency capacitors, resistors and inductors in the Ultra-High, Super-High and Extremely High Frequency range fall into the 1 Ghz to 300+Ghz range.
In terms of overall consumption of value-added and application specific passive components for high frequency applications, the largest segment will be for high frequency base station applications followed by medical test and scan equipment, including MRi and related scanning devices; defense communications for concentric warfare and related applications; and RF sputtering devices for semiconductor manufacturing, high frequency lasers and related industrial and laboratory test and measurement equipment.
The majority of demand for high frequency passive components in the UHF, SHF and EHF bands are for surface mount ceramic chip capacitors, thick and thin film resistors and wirewound chip coils. There is also demand for multilayered axial and radial leaded ceramic capacitors and single layered ceramic capacitors (especially thin film designs). It is extremely important to note that the single layered designs, have been developed because they extend into frequency ranges that are currently unattainable by multilayered designs (primarily into the EHF and millimeter wave bands). Key performance types consumed in this segment include NPO dielectrics, X7R dielectrics, low loss porcelain dielectrics and some Z5U dielectric designs. Thin film resistors manufactured from tantalum nitride and nickel-chromium resistor elements are also consumed in high frequency applications in such configurations as chips, networks and flatpacks. Thick film chip resistors that employ ruthenium oxide elements on ceramic substrates are also consumed in high frequency circuit applications as are specific types of carbon film resistors. A large portion of the discrete inductor market is dedicated to high frequency operation because of their use as electromagnetic compatabiluty components to prevent noise from interfering with outside devices.
High Temperature Passive Components: >125 Degrees C
The majority of all applications for high temperature capacitors, resistors and inductors are for under-the-hood automotive applications. This would include all class 3 to 8 on-road and off-road vehicles, although these usually max out at 150 Cdegree C operational environments, with 175 degree C now in experimental stage. There are also some transportation applications where the temperatures may reach to 250 degrees Celsius such as in the wheel-wells. The specialty markets that exist for very high temperature passive components go to 300 degrees C (and in some instances even higher) and are usually reserved for oil and gas electronics such as logging tools and downhole pumps; as well as aerospace and defense applications in rocket motors and satellites, as well as high speed aircraft and in geothermal electronics, and in some industrial furnace applications.
Automotive under-the-hood capacitors are almost all surface mount ceramic chips with respect to configuration and usually are in the X7R or X8R dielectric, depending upon the temperature requirement. For specialty high temperature applications, more radial leaded ceramic capacitor designs are thought to be sold in this segment of the marketplace, especially for sensor assemblies due to the high voltage handling capability of the radial leaded designs; but also there is increased demand for the large case size chips used in power supply assemblies for the same aerospace, oil well service and geothermal applications. Solid tantalum capacitors are also consumed in high temperature applications to 200 degrees C, and these are epoxy molded chip designs. Wet tantalum capacitors are also manufactured to withstand 200 degree C environments, and some hermetically sealed solid versions can withstand up to 230 degrees C. Some plastic film capacitors, most notably those manufactured from PPS film, can withstand operational temperatures up to 130 degrees C; however, the more exotic films manufactured from PTFE and Polyimide materials can withstand temperatures to 200 degrees C. More exotic and rare capacitors, such as those manufactured from mica and glass can also be used in circuits requiring temperature of up to 150 degrees C.
Thick film chip resistors employing ruthenium oxide resistive paste on alumina ceramic substrates can also be used in applications up to 230 degrees C, while wirewound resistors, which employ nickel chromium wire on an alumina mandrel can also be used to 230 degrees C; while sputtered nickel chromium on metal strips and ceramic substrates are also used for applications up to 275 degrees C.
Discrete inductors can also be manufactured to achieve high temperature operation to approximately 155 degrees C and are usually employed in under-the-hood applications. Such inductors are usually wirewound in nature and have molded out packaging to help withstand the heat.
Summary and Conclusion
Many passive component manufacturers today have distanced themselves from the price sensitive mass commercial markets in wireless handsets, computers and TV sets and have focused instead on the niche markets where premiums remain high and price is secondary to quality and reliability. This represents only about 13% of the market in terms of dollar value, but the premiums in these specialty segments remain high enough for many of the smaller vendors to remain profitable, even in hard economic times. Technical variations, including different dielectrics, resistive elements and substrates; configurations, and terminations and technical knowledge and advanced product engineering capability is required to succeed and thrive in the space. Paumanok Publications, Inc. has determined the specialty segment, known as value-added and application specific, is a growth market for the future, for those who have the technical aptitude to compete effectively today and to continue to develop components that can adhere and comply with the customer roadmaps that call for higher voltages, higher frequencies and higher temperature operation in the future.